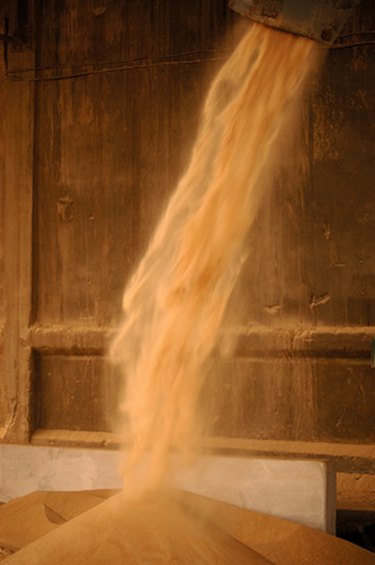
It starts with sand. Fiberglass is literally a fiber spun from molten glass, and silica sand is the main ingredient in glass production. Glass fiber is used in applications as varied as boat hulls and fire-resistant fabrics, but according to the National Association of Certified Home Inspectors, the predominant use for fiberglass is in thermal insulation.
History
Video of the Day
Glassmaking is an ancient art, but the techniques for producing the familiar pink woolly stuff that insulates our homes was only discovered in 1932 when a researcher accidentally sent a blast of high pressure air through a stream of molten glass. The resulting fine fibers were trademarked in 1938 as Owens-Corning Fiberglas (with just one "s"), and in 1987 Owens Corning trademarked the color pink. Today the term fiberglass has passed into the public domain. Other manufacturers have joined Owens Corning and use similar processes to spin glass fiber--in any color but pink.
Video of the Day
Recycled Glass
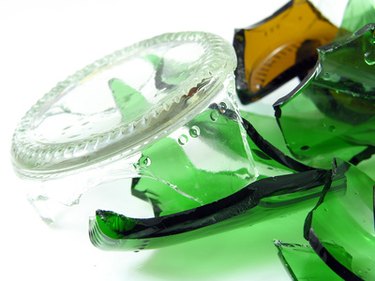
Molten glass intended for fiberglass production contains silica sand and other raw materials such as lime and soda ash in carefully measured ratios. Boron is added to make the glass fibers more flexible. Fiberglass also contains cullet--cleaned and crushed recycled glass. U.S. Environmental Protection Agency approval requires a minimum of 20 percent to 25 percent glass cullet use.
According to the North American Insulation Manufacturers Association (NAIMA), fiberglass insulation manufacturers make up the second-largest secondary market for recycled glass containers. This results in a product that saves 12 times the energy used in production within its first year of installation.
Production
Fiberglass insulation is produced in either blanket form or as loose fill. In both cases the automated process begins with molten glass flowing past a series of air jets that simultaneously spin out the fibers, coat them with a liquid binder, and break them into random short pieces. The cooling glass fibers fall onto a moving conveyor belt below, piling up into a tangled mass.
The conveyor carries this blanket of fiberglass through curing ovens, before it is cut to the desired width and length. A vapor barrier may be bonded to one side with liquid asphalt.
The binder agent is omitted if the final product is to be loose fill.
Labeling
Fiberglass insulation is identified and labeled by its resistance to heat transmission, known as its R-value. According to the NAIMA, common standard R-values range from R-11 to R-38. The higher the number the greater the resistance to heat flow. Batts and rolls will have the R-value stamped on the product and loose fill will have the information on the packaging.
Considerations
Formaldehyde may be used in the binder agent for blanket insulation. Most of the formaldehyde evaporates during the production process and is captured by pollution control equipment. Formaldehyde in fiberglass insulation is not a significant source of indoor air pollution, but there are products made with formaldehyde-free formulations, listed with Greener Builder.org.
- North American Insulation Manufacturers Association: Sand
- North American Insulation Manufacturers Association: Health and Safety Facts for Fiber Glass
- National Association of Certified Home Inspectors: Fiberglass Insulation – History, Hazards, Alternatives
- U.S. Environmental Protection Agency: Building Insulation
- National Park Service: Environmental Considerations of Building Insulation
- Owens-Corning: A Heritage of Innovation
- Certainteed: Insulation
- Johns-Manville: Healthy, Safe and Sustainable Solutions