Things You'll Need
Electric saw
Router
Drill
Palm sander
Utility knife
Grease pencil
Double-sided masking tape
Straight edge
Scrap lumber
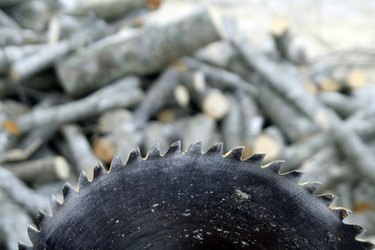
High-density polyethylene, or HDPE, is an extremely popular plastic used for everything from cutting boards to boat parts. Its low friction makes it a comparable replacement for Nylon or Teflon. HDPE is also generally less expensive that Nylon or Teflon. It is easy to machine and, unlike acrylic, will not crack when being cut. Using conventional shop tools, HDPE can be machined into a number of useful parts.
Step 1
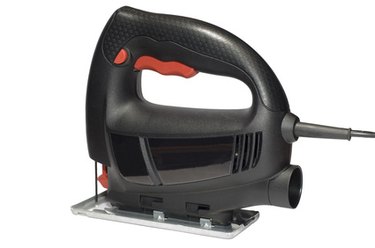
Cut the HDPE to the desired size with a table saw, radial arm saw, circular saw or jig saw. The key to a good cut is to use sharp blades and a proper feed rate. The feed rate is how fast the material is pushed through the saw. If the piece is cut with a dull blade at too slow a feed rate, the material can melt against the blade. Use a 60- to 80-tooth, carbide-tipped blade. The feed rate should be roughly 70 to 90 feet per minute.
Video of the Day
Step 2
Route cutouts or channels using a carbide router bit. Carbide bits last longer than standard bits when used for cutting plastic. If the router has an adjustable speed, set it around 18,000 rpm. The feed rate should 8 to 16 feet per minute. For straight cuts or square cutouts, create a guide made from scrap lumber or plastic for the router to follow. Measure the distance from the bit to the outer edge of the router's bottom plate or collar. This is the distance to use when placing the guide. Apply double-sided tape to the guide to hold it on to the material. For cutouts, drill a pilot hole larger than the router bit, rather than plunge routing into the plastic.
Step 3
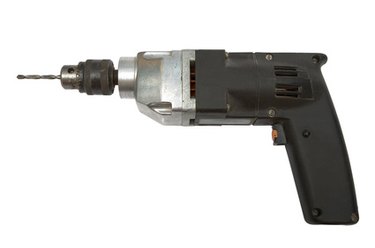
Mark any drilling locations using a grease pencil. This type of pencil will adhere to the HDPE whereas lead pencils will not. Use a drill bit with a 45- to 60-degree point. Flat drill bits tend to skip across the material rather than biting into it. The drilling speed should between 3,500 rpm for thinner material--1/8 inch--and 450 rpm for thicker material--1 inch. Drilling speeds are not as critical for HDPE as they are for harder plastics such as acrylic. HDPE is soft enough to drill without any lubrication.
Step 4
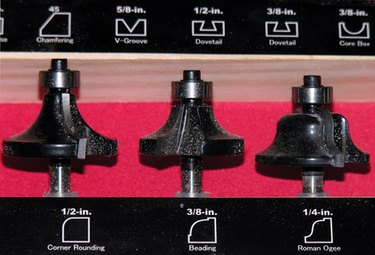
Sand down material to finish the edges with 320-grit sandpaper. HDPE is softer than most plastics, therefore it sands faster than materials such as acrylic. For a clean or sharp edge, use a utility knife to scrape the material smooth. Hold the blade at a 60-degree angle to the material and lightly push the blade outward. Make sure there are no jagged edges that will catch the knife.
Tip
HDPE is extremely difficult to glue. Therefore, using screws to join pieces together is best. Double-sided masking tape works well for temporarily joining HDPE.
HDPE has a low melting point so it can be heat-formed in the same way acrylic can.
Video of the Day