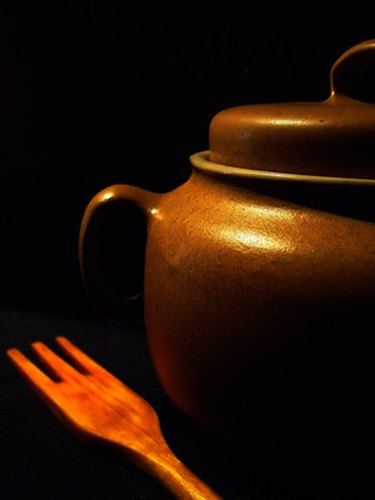
Ceramic glazes are both useful and decorative. Unglazed ceramics are porous. If liquid is left in an unglazed vessel, it will leak out through the open clay pores. Glaze coats ceramic surfaces, making them impermeable and waterproof. Glazes are also an expressive medium for artists.
History
Video of the Day
Tracing the origins of glaze sheds light on various customs and cultures. According to the History World website, the Greeks developed fired unglazed earthenware for storage and cooking in the 5th century BC. The pots were porous and unable to hold water until the development of glazes in the 1st century BC in Egypt. The first blue-green glassy glaze is commonly known as Egyptian paste and is still popular today. Glazed ceramics were simultaneously developed in early China and the Middle East, and traded along the Silk Road. Glazed ceramics were coveted commodities and the active exchange of ceramic styles and techniques impacted future development of the craft. Early European pottery and glaze techniques were influenced by eastern ceramics that traveled to Rome.
Video of the Day
Decoration
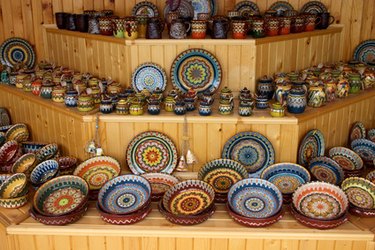
As stated on HistoryWorld.net, Greek potters perfected a decorative style of glazing that is still popular today, involving direct application of black and red iron oxides to clay surfaces. Oxides are mixed with water and painted on with brushes to achieve a pen-and-ink effect that withstands firing at high temperatures. Greek potters created elaborate oxide decorations on vessels and tiles, often depicting human and animal figures. Oxides are used both under and over applications of clear glass glaze for coloration and decoration. Today, oxides are mixed with other glaze chemicals and available for potters at ceramic supply stores and online. These products are called underglazes (for application under a glassy glaze) or overglaze (applied on top of a glaze and refired.) Each one has a different decorative outcome. Glazes are silica-based glass that creates a smooth, glass surface over clay when melted at high temperatures. Commercial glazes contain several key components including: a glass former, such as silica; Flux, a melting agent that enables silica to melt a lower temperatures; refractories, stiffening agents that enable flowing glass to adhere to a ceramic surfaces; and colorants, such as oxides. Silica is clear and slightly green until metallic oxides are added to modify the color. A wide range of decorative glazing products are available today.
Waterproofing
At extremely high temperatures--generally between 1800 and 2400 degrees F--in a ceramics kiln, glaze melts and flows evenly over an object, coating the surfaces evenly with a thin coating of glass. As the glass cools, the glazed surface turns smooth and solid. The result is a tight surface that is impervious to water and holds liquids effectively over time. Care must be taken to coordinate expansion and shrinkage rates of glaze, and the underlying clay or cracking and crazing will occur during the heating and cooling process.
Strengthening Clay
Glaze strengthens the entire body of a ceramic vessel. Potters calculate glaze fit (the relationship between glaze and underlying clay) so the fired glaze fits tightly on the ceramic surface, thereby compressing the clay molecules. Compression results in greater resistance to liquids and increased durability of the object.
Glaze Application
Glazes are generally applied as liquids to a ceramic surface by painting or dipping an object into a bucket of glaze. Glazes and oxides can be rubbed into ceramics as dry powders. A process popular in Europe in the 17th and 18th centuries involves tossing salt or sodium bicarbonate into a kiln near the end of the firing process. The salt vaporizes and merges with the surface of the clay, forming an interesting mottled glaze. This process is known as salt or soda glazing. According to CeramicArtsDaily.org, soda firing is the technique most used by potters today, usually in gas-fired kilns.