Things You'll Need
Sandcloth
Wire fitting brush
Latex gloves
Flux
Acid brush
Safety glasses
Leather gloves
Solder
Gas torch
Fire extinguisher
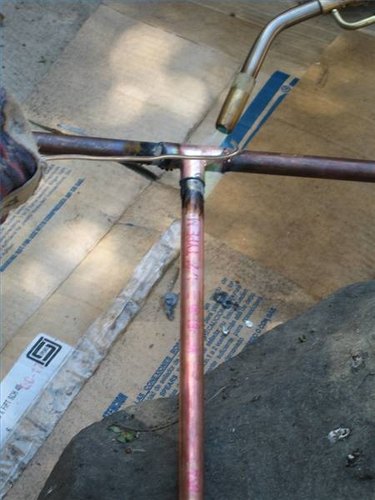
Flux and solder are commonly used when soldering copper water pipes. Flux is an acid that you use on copper before soldering to remove oxides and prevent the metal from oxidizing further when you heat it. The lack of oxide allows the solder and metal to melt together and form an alloy, which means that the solder and copper have become one seamless piece of metal. Follow the steps below to learn the proper way to use flux when soldering.
Step 1
Use sandcloth to polish the pipe you will be soldering, whether it looks dirty or not. Drape the sandcloth over the pipe and lightly squeeze with your fingers while rotating the pipe with your other hand.
Video of the Day
Step 2
Clean out the inside of the female fitting using the wire brush. Test fit the fitting and pipe.
Step 3
Put on your latex gloves. Use the acid brush to put a healthy amount of flux around the outside of the pipe. Apply a smaller amount evenly inside the fitting all the way to the bottom.
Step 4
Join the pipe and fitting together and use the brush to wipe off any excess flux at the edge of the fitting.
Step 5
Unroll about 6 inches of solder and bend the last two inches to a 45- to 90-degree angle. Put on your safety glasses and switch your latex gloves for the leather ones.
Step 6
Light the torch and put the tip of the flame on the fitting. Move it back and forth around the fitting for about 30 seconds until you see "sweat" on the pipe.
Step 7
Remove the flame from the fitting and touch the solder to the joint. Move the solder around the edge of the fitting as it melts. The joint is full when a drop of solder drips from the bottom. Let cool.
Warning
Use a flame shield, such as sheet metal, between the pipe and any flammable materials.
Video of the Day