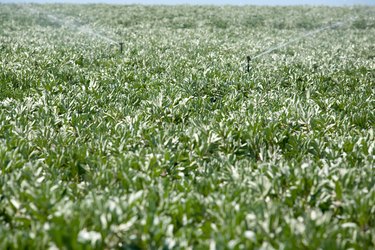
The Rain Bird R-50 Turf Bird is a popular sprinkler model that has since been discontinued, but you may find yourself needing to adjust an existing installation. The unit can be adjusted both in terms of water flow and the arc it traces.
R-50 Turf Bird General Information
Video of the Day
The R-50 Turf Bird can be set to a range of arcs without the use of tools, including full circle (360 degrees) or smaller arcs between 25 and 350 degrees. The R-50 Turf Bird comes preset to a half circle, or approximately a 180-degree arc. The left side of the arc is fixed, with the sprinkler turning from that position to execute the arc.
Video of the Day
Therefore, when installing or adjusting the sprinkler, make sure to align the left side of the arc with the area you desire to irrigate. This fixed position can be identified by finding the double ribs on the outside of the body (see the illustration in your manual). Keep in mind that it is possible to turn the entire sprinkler after it has been installed on its fitting.
Note that the full circle and part circle settings induce different behaviors and irrigation coverage. When the sprinkler is set to full circle, it rotates fully in only one direction in a continuous repeating circle. When the R-50 Turf Bird is set to a partial arc, however, it covers the arc in one direction and then reverses and traces the arc again in the other direction. Take this behavior into consideration when placing the R-50 Turf Bird sprinklers and planning the irrigation pattern for your lawn or garden.
Rain Bird R-50 Turf Bird Adjustment
The two main adjustments on a Rain Bird R-50 Turf Bird are the bypass and the arc. The bypass controls the flow of water through the drive mechanism to the nozzle, while adjusting the arc controls the spread of the water. Adjusting the bypass requires a screwdriver, but adjusting the arc can be accomplished without tools.
Before adjusting the bypass, ensure that the position of the bypass matches the size of the nozzle (see the diagram in your manual). To adjust the bypass, hold the sprinkler inlet with one hand and use your other hand to insert a flat-head screwdriver into the slot at the bottom. You can then turn the slot to align with the setting you want based on the nozzle size. Turning it clockwise will increase the flow.
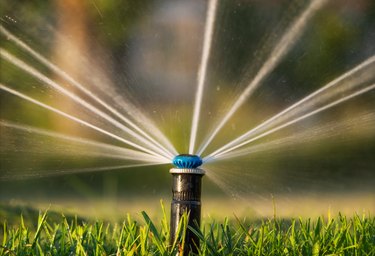
To adjust the arc in a partial circle, first check that the left (fixed) edge of the arc is in the desired position per the double ribs on the body. Then, when the sprinkler is operating, grip the vandal collar. You will want to slide it down the riser shaft without removing it. Hold the riser in one hand with the other pushing down on the nozzle. To increase the range of the arc, turn the nozzle turret clockwise and turn counterclockwise to decrease the arc. Return the vandal collar to its original position once you have completed the adjustment.
Changing Settings on the Sprinkler
If you wish to switch the R-50 Turf Bird sprinkler head to full-circle mode, you will need to remove the internal assembly from the case. Recall that this adjustment will switch the sprinkler from a back-and-forth motion to a continuous circle motion. Unscrew the cap and spread the vandal collar before pushing it down. Push down the nozzle turret and make sure the vandal collar gap decreases to show you have switched to adjustment mode.
While holding down, turn the nozzle fully clockwise until you feel a strong resistance, as if the nozzle is locked into place. After releasing the nozzle and returning the vandal collar to its original position, verify that you have switched to full-circle mode by turning the nozzle clockwise. You should not feel any resistance anywhere while turning the nozzle all the way in a circle.
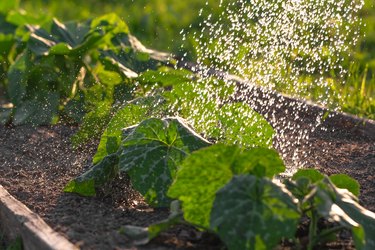
To switch back to partial arc mode, open the vandal collar and push down on the nozzle turret. While pushing down, turn it to the right past the trip, at which point you will be defining a new part-circle arc.