Things You'll Need
Flashlight
Tripod
Winch
Multimeter
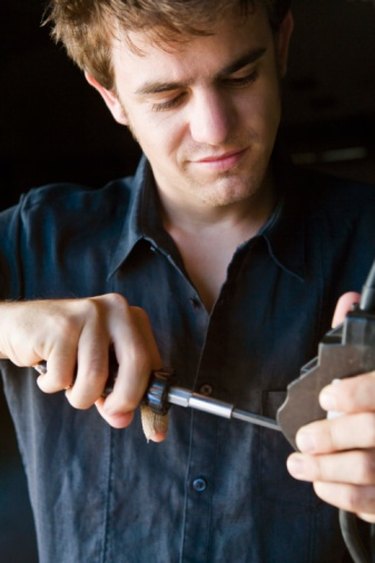
Remove the pump and associated piping from the well to repair a deep-well submersible pump. The pump is made up of a motor and an impeller. It may also have a check valve to prevent back-flow and a tail pipe attached below the pump. Start with a visual inspection and then apply electrical and mechanical tests to find which particular component is damaged. Once the damage is located, the entire damaged unit may have to be replaced or, if the damage is confined to a small part like a seal or a protective cover, that part may be replaced.
Step 1
Turn off the power and lock out the breaker or disconnect switch. Remove the well cap and shine the flashlight into the shaft. You'll have to disconnect the pitless adapter and pull up the pipe, electric cable and pump. Look for a pipe, chain or rope that was used to lower the pump into place. Use it to raise the pump and pipe, and make the pitless adapter slide out of its holder. Otherwise, place a chain under the pipe elbow leading to the pitless adapter and haul up the pipe. Small wells with pumps less than 1/2 horsepower, pipes 1/2 inch or less in diameter and less than 100 feet long can be lifted out by hand. Larger units are too heavy and need a tripod and winch to haul out.
Video of the Day
Step 2
Inspect the pump visually. Check for wetness on the pump and pipe string to make sure the pump is actually submerged. If not, you will have to add pipe to situate the pump deeper in the well or drill the well itself deeper.
Check for obvious damage. There may be mechanical damage caused by debris in the well. Such damage can often be repaired by replacing the cover or casing of the pump. The check valve or tail pipe may be clogged and can be freed.
Step 3
Check for electrical motor damage. Remove the motor cover where the cable enters the motor. One of the cable wires connects to the starting capacitor. Switch the multimeter to resistance testing and connect across the capacitor. The needle should jump. If it doesn't or if the meter reads zero resistance, the capacitor must be replaced.
Check the motor resistance. An open circuit means that there is a bad connection or a winding, or connection has burned through. A zero resistance means the motor has shorted out. In either case, the motor must be replaced.
Step 4
Check for mechanical problems with the impeller. Use a screwdriver to turn the motor to see if the impeller turns freely. If not, open the impeller casing and remove the obstructions. Check the impeller for cracks and check the seals at either end for wear or gaps. If there is mechanical damage, the impeller itself or the whole impeller unit must be replaced.
Reassemble the repaired unit and lower the pump and pipe back into the well. Make sure the pitless adapter engages when the pump is in position. Close the well cover.
Video of the Day