Things You'll Need
Transfer design
Plastisol ink
Screen printing press
Nonpermeable emulsion
Squeegee
Heat transfer paper
Curing unit
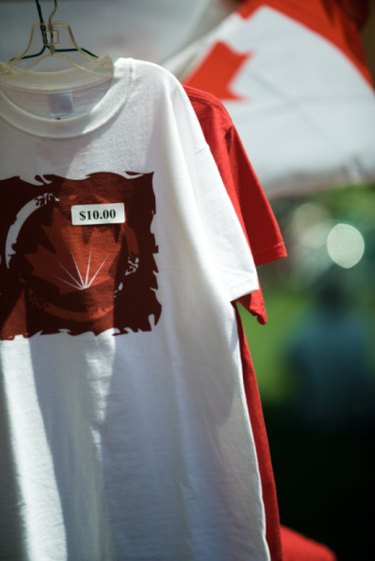
Plastisol is a special PVC-based ink which is printed onto heat-transfer paper to create a transfer of the design. You can then apply the transfer to clothing using a heat press. Unlike many printable transfers, Plastisol can easily print a design onto dark fabric. After the transfer, the Plastisol ink will have a slightly raised or puffed appearance and can last for several years with proper care. Unlike simple ink transfers, Plastisol transfers can't be printed using a home printer. You'll need specialist screen-printing equipment.
Step 1
Choose or create the design you want. You can sketch it out with pencil and paper, or create the image using a computer. Because of the way Plastisol ink gels as it cools, some designs will not print clearly. Avoid fine lines or large areas of solid color. Lines should be no thinner than 1/16 of an inch. Create a mirror image of your design, because the Plastisol transfer will be flipped over when you apply it to the garment.
Video of the Day
Step 2
Choose your ink. There are a number of Plastisol inks available. Plastisol ink comes in tubs of varying sizes, and can be purchased from most stores that sell screen printing supplies. You will achieve the best results with an ink specially formulated for transfer printing. You may wish to add an adhesive powder to the ink to make the transfer easier to apply.
Step 3
Create a stencil of your design, and lay it over the mesh layer of your screen printing press. The method of creating the stencil will vary depending on your press, but usually involves painting an outline of the design in nonpermeable material. The thickness of the mesh should be between 3 and 6 millimeters, and the mesh should be about 86 to 120 threads per inch. Apply the Plastisol ink to the mesh. Although screen presses vary, in most cases you will apply the ink by filling a reservoir with it and then drawing the fill bar across the mesh to spread ink over the screen. Using a squeegee, press the design onto the heat transfer paper. Some types of heat transfer paper have coated and uncoated sides; make sure you apply your design to the coated side. If in doubt, refer to the paper packaging. If your design has multiple layers of color, apply the dominant color or the black outline first, then smaller areas of color. If possible, avoid superimposing layers of color, as this can make the ink dry unevenly.
Step 4
Cure the transfer. You'll get the best transfer if the transfer cures evenly. Blow dryers or other small heat sources produce uneven curing and should be avoided. A commercial dryer such as a conveyor dryer is your best choice for a curing unit. The temperature will be based on the ink and paper you have used in your transfer, but it will usually be 180–250º Fahrenheit. Consult your ink's packaging for the correct temperature. Curing times vary depending on the heat source and the size of the transfer. Once it's cured, which can take no more than a few seconds, your Plastisol transfer is ready to apply.
Tip
Paper shrinkage can sometimes be a problem, especially when printing multiple colors. You can reduce this risk by running the paper through the dryer first, effectively pre-shrinking it.
Video of the Day