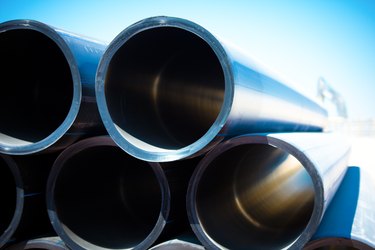
Welding HDPE, or high-density polyethylene, is a normal procedure for joining lengths of pipe together for industrial or home use. One of the benefits of welding HDPE plastics in smaller applications such as you might find in home plumbing systems is that no weld filler rod is necessary. Simply heating the HDPE to the correct temperature and then fusing it together with the other piece is usually sufficient to fully weld the two pieces together. The catch is that you can't use a hair dryer to obtain the correct temperatures you'll need for the process.
Things You'll Need
Video of the Day
How to Weld HDPE
Step 1: Lay the Pipes on a Flat, Heatproof Surface
Lay the HDPE pipes on a stable work bench or a surface that will not be affected by heat. In the field, plumbers might use sawhorses, a flat area of ground, or the installation point as a work area.
Video of the Day
Tip
You can use a bench vise to hold one of the pieces or, if you are working in an area where you cannot access a bench vise, you can weld the HDPE pipe on a concrete floor. Avoid performing this work on linoleum or wood floors, as the extreme heat can damage these types of softer finishes. Performing this work on a floor or a workbench before the pipes are installed will allow you to more easily control the final shape of the pipe without having to hold it in place by hand. Welding the pipes on the floor and then leaving them alone is sufficient to obtain a strong bond.
Step 2: Wipe Down the Surfaces to Be Welded
Apply rubbing alcohol to the HDPE surfaces that you are going to weld together; then wipe each with a clean rag. This will remove surface oils and other debris that can contaminate the weld.
Step 3: Use a Heat Gun to Soften the Surfaces
Lay the two pieces beside one another with the points at which they will be welded within an inch or two of one another. Use a heat gun to heat the two surfaces that you'll be welding to a temperature of approximately 572 degrees Fahrenheit (300 degrees Celsius). At this point, HDPE becomes extremely soft and pliable. Do not touch the areas to test their pliability or heat, as the plastic surface at this temperature can stick to your skin if you touch it and cause extremely severe burns. Instead, use a noncontact thermometer to determine the surface temperature of the HDPE parts.
Step 4: Press the Heated Surfaces Together and Let Cool
Lay the heat gun aside and then press the heated work pieces together at the point at which they are to be joined. The HDPE will ooze slightly at the joint on both pieces. Allow the two pieces of HDPE to cool for three minutes while you hold them in place and wait another 10 minutes before applying pressure to the welded joint or attempting to install the pipe. When the two pieces of HDPE have cooled to below 120 degrees Fahrenheit (49 degrees Celsius), the HDPE plastic parts will be fused together. At this point, you can install the new piece or continue your project as applicable.
Tip
For industrial uses, such as with pipe measuring more than 12 inches in diameter, it may be a good idea to use an HDPE fusion welding electrode rather than a heat gun. Heat guns work well for home plumbing repairs and construction but are less effective in industrial situations.
Warning
Avoid touching the heated plastic with your hands or body parts to avoid burns. Even touching the heated plastic with gloves could cause contamination of the weld area.
- Arwin Mathias: HDPE Pipe Welding Using Heat Fusion
- HDPE Jointing Works: HDPE Pipe Jointing in Torch Welding (Heat Gun)
- King Plastic Corporation: Methods for Welding HDPE
- Colorado Plastic Products: A Look at Hot Air Plastic Welding
- King Plastic Corporation: Tips for Welding Thermoplastics
- HDPE Supply: Heat Fusion Joining Procedures: PolyPipe by Dura-Line